axle|MOBILE is the ideal portable weighing system for those who need to accurately measure the weight and weight distribution of vehicles up to 20000kg per axle, such as truck and special vehicle manufacturers, vehicle and trailer modification workshops, etc.
axle|MOBILE is also an indispensable tool for all companies that put transport vehicles into operation, enabling them to ensure that the load distribution of all vehicles complies with current regulations and maximum transport safety conditions.
The axle|MOBILE portable weighing system is designed to measure with extraordinary precision the weight per axle, automatically obtaining the total weight of the vehicle as the sum of the axle weights. It can operate in static mode, positioning each axle successively on the scale, or in dynamic mode at low speed, without stopping the vehicle at any time up to speeds of up to 8km/h.
It can be installed and uninstalled on the ground by a single person in less than 20 minutes, without the need for a pit. All that is required is a sufficiently large, flat and resistant surface such as the usual truck circulation areas. It is made of stainless steel and aircraft grade aluminium, guaranteeing our usual ultra-rigid performance and the durability that characterises all our weighing systems. The modular levelling tracks (2-metre rolling elements), made of high-strength composite polymer, is designed to be light, strong, easily transportable and to take up minimum space when stored rolled up.
THE LOAD RECEIVING PLATFORMS
The scales or load receptor platforms are made of machined, seamless, aeronautical grade aluminium monobloc. The choice of material, as well as the elaborate internal structure, ensures a rigid behaviour when applying the nominal load of 10000kg/platform (20000kg/axle) on a surface equivalent to the tyre footprint, avoiding the appearance of non-vertical force components and the fatigue of the materials due to the use of the system. This design allows to provide the weighing system with a much longer lifetime than other traditional solutions.
The sensors chosen to equip each platform are high-end HBM RTN torsion ring load cells, mounted in a kit capable of absorbing any small slopes at the system’s location. The use of the highest quality load cells in the industry increases measurement accuracy and instrument longevity, ensuring that the platforms can be adjusted year after year, during regular maintenance, indefinitely.
The LEMO connectors fitted to the platforms are of outstanding quality, equipped with self-centring and self-locking mechanisms. The carrying handle and built-in wheels allow for effortless installation.
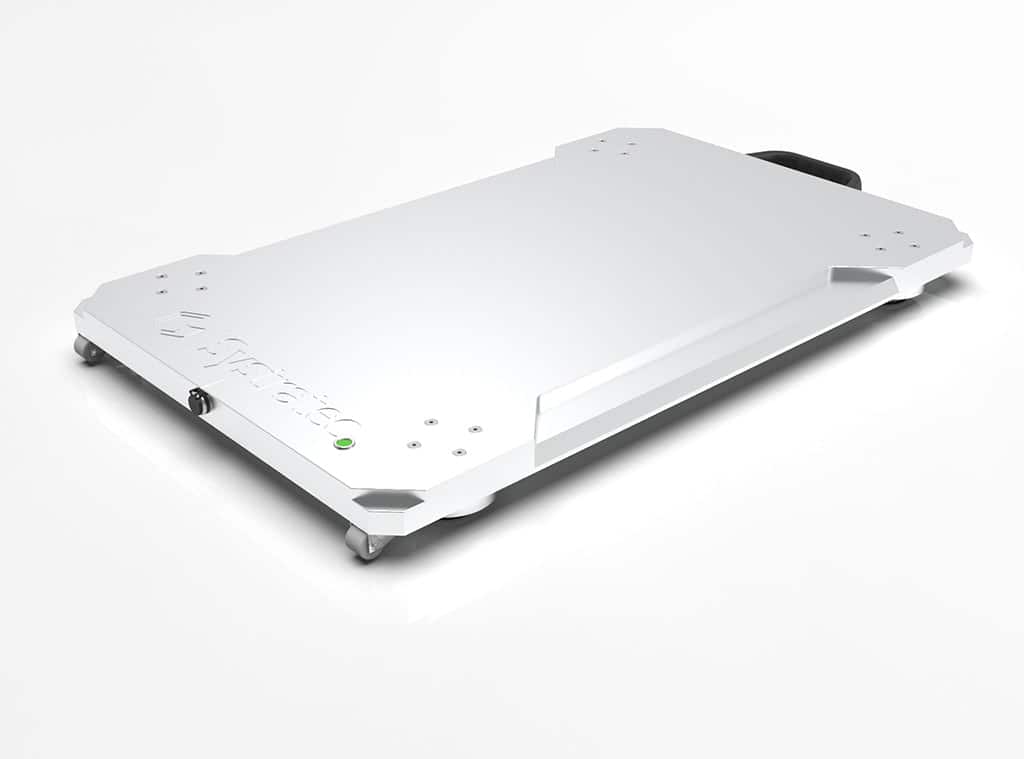
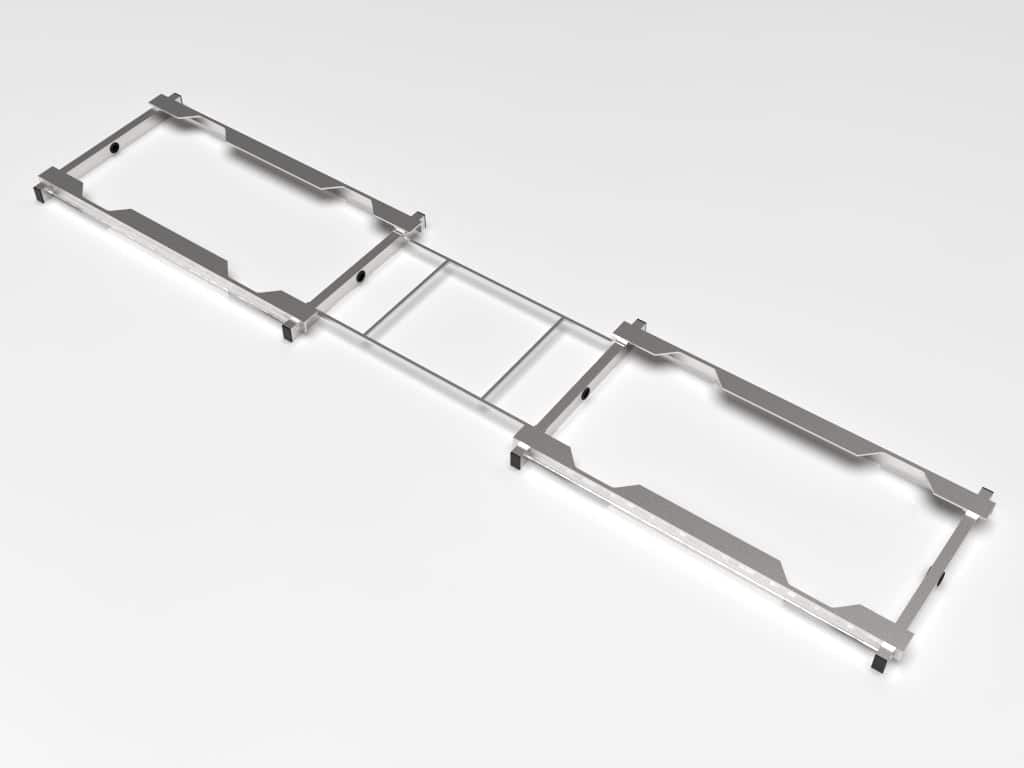
THE POSITIONING FRAME
The positioning frame is a modular structure made of high-strength stainless steel. Its basic function is to establish the position in which the platforms are to be installed at their place of use. Its advanced function is to perform the proper transfer of the load between the raceway and the platforms, which is particularly important when the system is used in dynamic weighing mode.
In addition to this, its design, in collaboration with the design of the platforms, prevents platform tilting when the vehicle load is transferred onto the platform from the raceway. Avoiding this rocking is essential to ensure a long service life of the system and the maintenance of its accuracy over time.
It also serves as an anchoring element for the levelling tracks and as a protective structure for the wiring. In addition, it is easy to handle and install and can be stored in a minimum of space.
THE LEVELLING TRACKS
The levelling track is an essential part of portable axle weighing systems. Its function is to keep the vehicle level during the weighing of all its axles. The minimum length of track required is that which allows each rigid section of the vehicle to be kept perfectly level during the weighing of its axles. For example, in weighing trucks with trailers, we must always make sure that no axle of the tractor unit is outside the wheel track during the weighing of the axles belonging to it and, subsequently, make sure that all the axles of the trailer are always on the track while they are being weighed sequentially. The raceway must always be of identical length in front of and behind the weighing system.
At SYSTRATEC, we have designed our levelling tracks in connectable modules, so that it is easy to always have the required length depending on the types of vehicles to be weighed. Each module has an extended length of 2 metres, and may or may not have built-in access ramps, depending on whether it is an access/exit section of the system or a connection section to the weighbridge.
The road elements are composed of multiple pieces of high-strength, thermally stable polymer composite, manufactured by injection moulding, with an extraordinarily elaborate shape to combine lightness, durability and load capacity. They are joined together by steel cables that weave each section so that it can be easily rolled up for storage and transport.
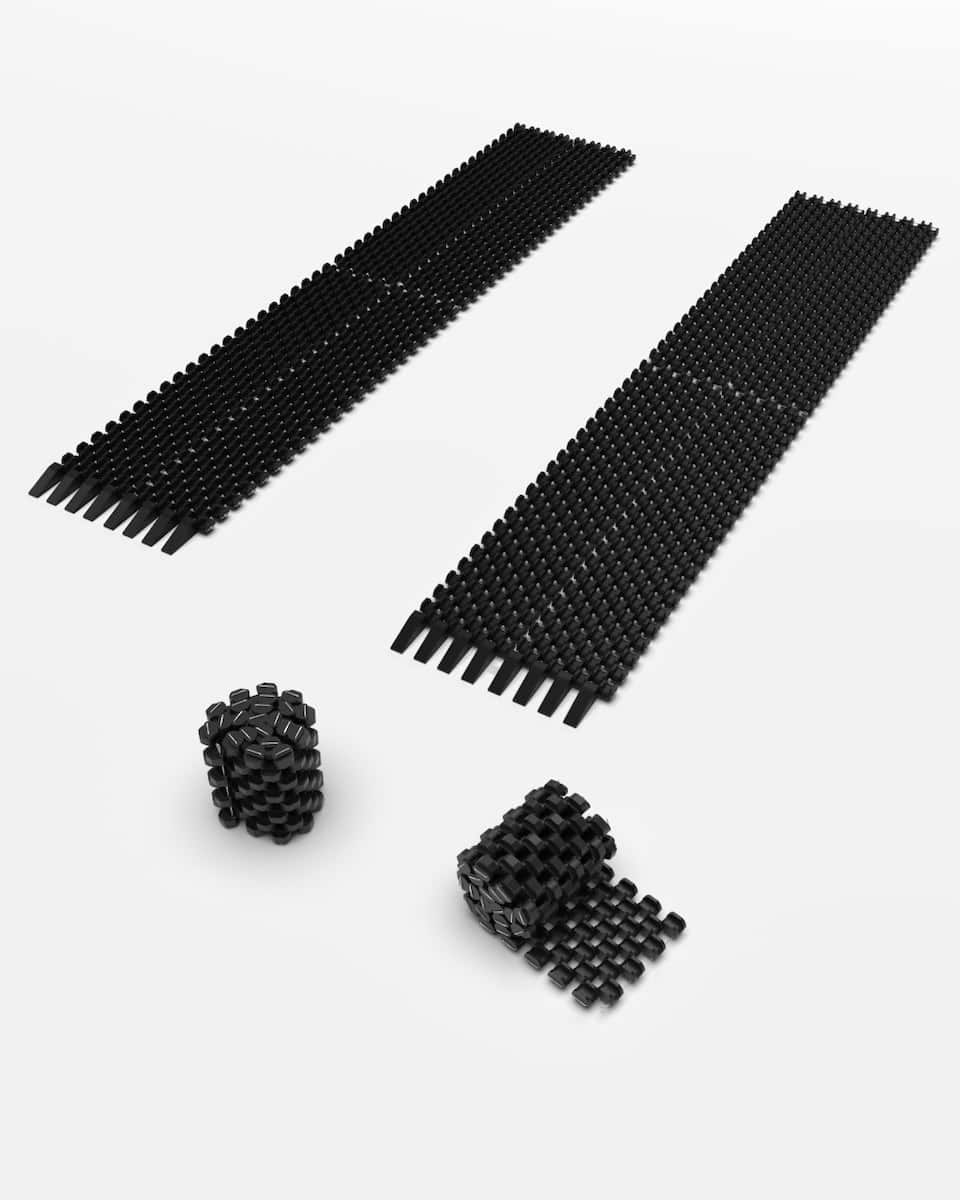
INSTALLATION DIMENSIONS
The most common arrangement of the components of our axle|MOBILE portable axle weighing system is the one used for weighing articulated lorries with trailers, as shown in the figure below:
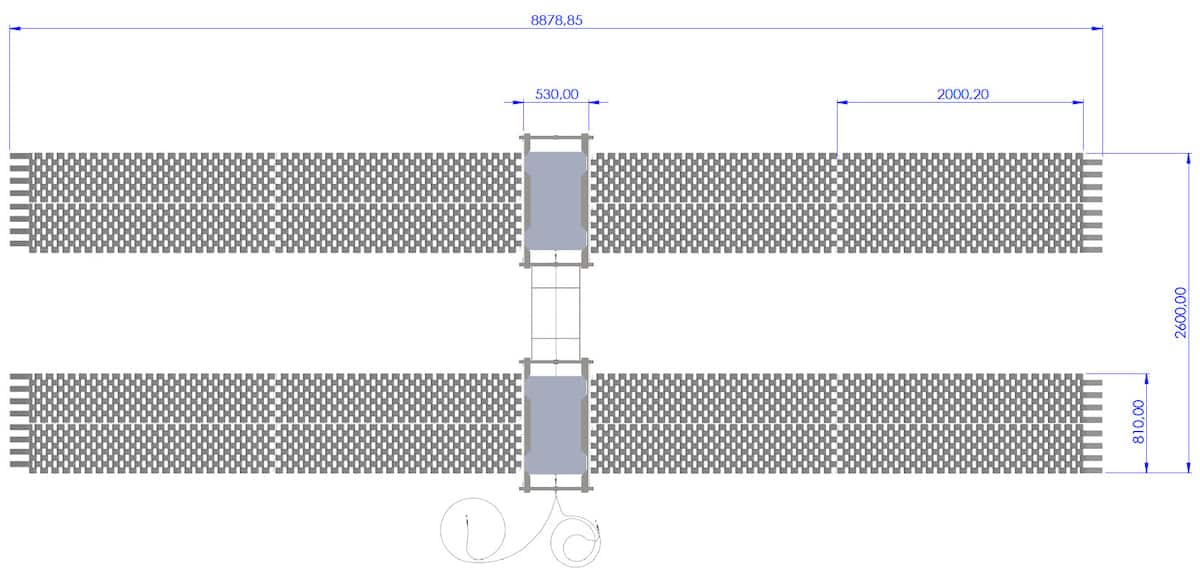
The installation shown occupies an area of approximately 9×3 metres. The ideal surface should be level, free of gravel and resistant to the pressure exerted by the system. This system layout requires the following ordering elements:
- Two SYSTRATEC axle|MOBILE platforms
- One positioning frame assembly
- Eight entry/exit levelling track elements with ramps
- Eight scale connection levelling track elements
- One SYSTRATEC axle|REFERENCE Electronics
- Two 15m measuring cables
THE INSTALLATION PROCEDURE
The installation of our portable axle-by-axle weighing system for trucks is a simple process. It can be done by one person in 20 minutes. Watch the 90-second video below to find out how to install this innovative scale.
SYSTRATEC AXLE|REFERENCE MEASUREMENT AND DISPLAY ELECTRONICS
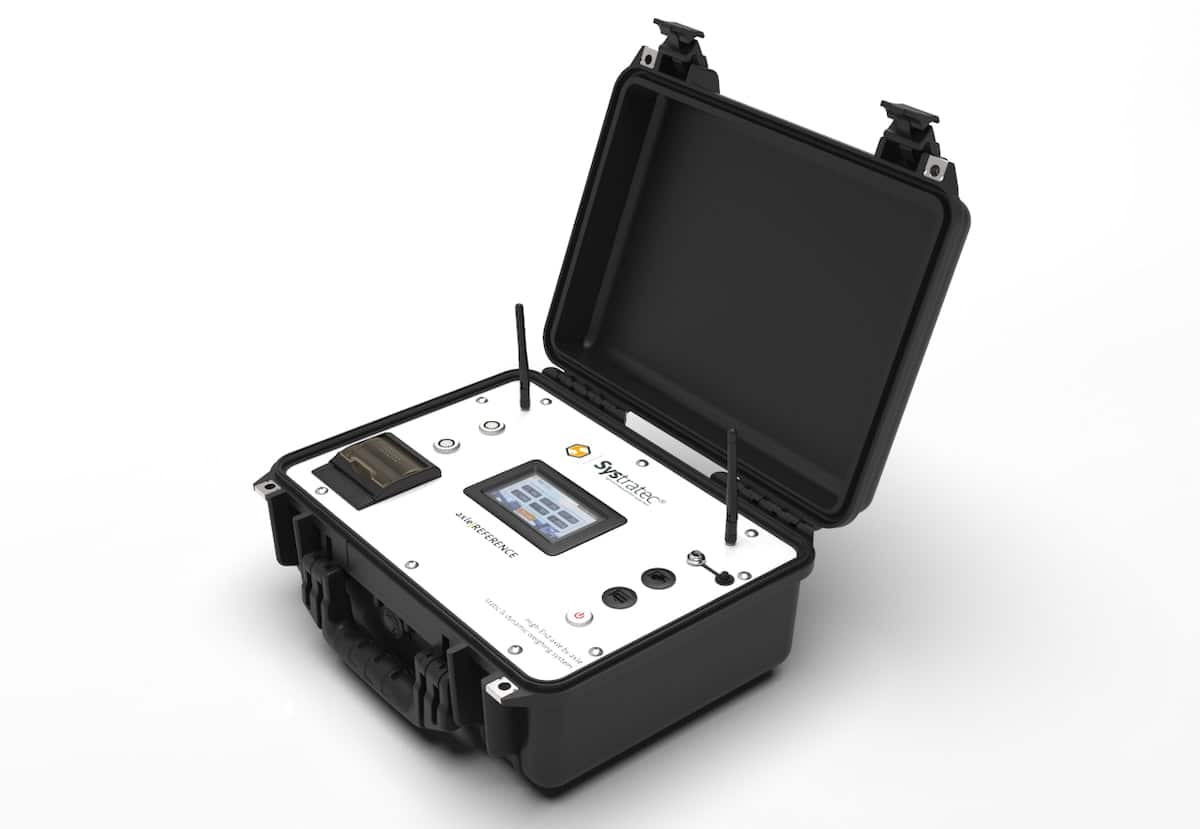
Our axle|MOBILE portable scales are designed to provide maximum performance in combination with SYSTRATEC axle|REFERENCE measurement and display electronics. These electronics are part of our Reference family, all sharing the same heart: a Systratec CORE processing unit and several Systratec LC-GRID load cell acquisition units, all perfectly encapsulated in a watertight military-grade case for safe handling, transport and storage.
The acquisition of the signals from each load cell is carried out individually by a noise-free 24-bit sigma-delta converter, having been pre-conditioned by hardware-fixed gain, zero-drift instrumentation amplifiers. There are as many independent and simultaneous acquisition channels inside the electronics as there are load cells in the system (eight).
Subsequently, the Systratec CORE processor board is responsible for converting the values obtained from the sensors into weight, using the calibration tables for up to 10 sections stored in its internal memory. In addition to this, in dynamic weighing mode, it performs calculations on the speed of each axle and the distance between axles to detect anomalous acceleration values that could compromise the accuracy of the measurements.
This processor board is also responsible for managing the full-colour TFT touch screen from which the system is controlled and the thermal printer that allows a ticket to be obtained at the moment the weighing is carried out.
The communications options implemented in the electronics enable the integration of the data measured by the scale into the customer’s industrial environment.
The complete system is powered by an internal rechargeable LiFePO4 lithium polymer battery, with a charging time of less than one hour and a continuous working time of more than 8 hours.
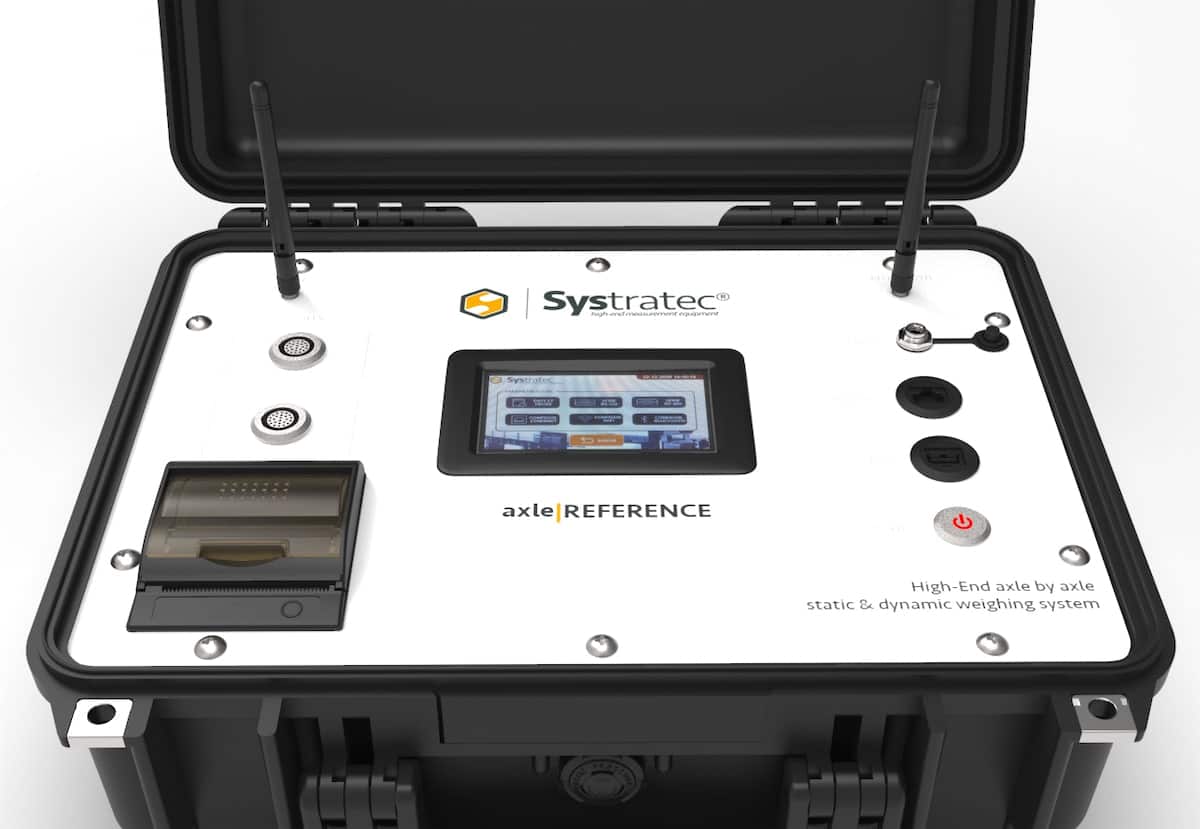
THE WEIGHING PROCEDURE
STATIC WEIGHING:
In this mode of operation, the vehicle driver shall position the first axle on the scales, bringing the vehicle to a stop. During axle weighing, the brake shall not be applied.
The weighing system operator shall accept the axle weight value measured by the scales when it is stably displayed. Once this partial weight has been stored, he shall instruct the driver to position the next axle on the scales to repeat the operation.
Once all axles have been measured, the vehicle will leave the scales and the system operator can obtain the total weight and the ticket with all the measured data. The accuracy of axle weights measured by this method is better than 99.9%.
DYNAMIC WEIGHING:
In this mode of operation, the vehicle driver must drive over the weighing system at constant speed, without accelerating or braking at any time, typically with power provided by engine idling.
The electronics automatically measure the weight of each axle and provide the total, alerting the system operator that the weighing is complete and that he can obtain a ticket with all the data measured at that moment.
This method provides an optimised logistical operation by reducing the weighing time to a minimum, in exchange for a slight decrease in the accuracy obtained. Typical accuracy of weights measured by this method is better than 99.5% on 95% of samples.
The following video shows the dynamic axle-by-axle weighing procedure of a five-axle articulated lorry with trailer. An illustration of the weighing ticket is superimposed, with the information that the system collects.
WHAT MAKES US DIFFERENT?
The desire to surpass traditional weighing technologies, building the most advanced, accurate and longest-lasting weighing systems on the market, is what drives the entire SYSTRATEC team. This ambitious objective is achieved by working on each scale in depth, seeking excellence in all the technologies used: the structural design, the choice of materials, the sensors used, the hardware of the measurement electronics and weight displays, the firmware of all the electronics, the calibration procedures and tools and countless other details. It is by taking the utmost care with each instrument, load receptor and electronics that we can guarantee our customers that the investment they have made in the purchase of their measuring equipment is protected and profitable by having an instrument that can be upgraded for many years and that is always capable of providing the highest quality of measured value in the industry. SYSTRATEC weighing and centre of gravity measurement systems incorporate the following unique technologies:
ULTRA-RIGID STRUCTURES
We build our scales and all our load receptors using only aerospace grade aluminium, stainless steel and carbon fibre. Our structures are designed to have zero deflection at nominal load over the tyre footprint. This results in greater linearity, accuracy and durability of all our instruments compared to traditional solutions.
FULL FIRMWARE CONTROL
As manufacturers of our own electronics, we have full control over the internal firmware. This allows us to offer the market a very high capacity of adaptation and integration of our instruments in any customer’s process. It also allows us to update our instruments throughout their useful life, evolving their capabilities as our customers’ needs evolve.
ERGONOMICS BY DESIGN
We design our scales under strict ergonomic requirements, always seeking to ensure that the weights suspended by the personnel in charge of their installation are as low as possible, while guaranteeing the durability that characterises our brand.
HIGH-END WEIGHT SENSORS
We build our scales and load cells around high-end stainless steel sensors based exclusively on strain gauges. Partners since 2015 with the German sensor manufacturer HBM® Hottinger Brüel Kjaer, we exclusively use these load cells for their outstanding metrological quality and durability, which are recognised worldwide and present in all reference laboratories. The use of these high-end load cells allows for greater ease of adjustment year after year, virtually indefinitely, compared to other technologies such as piezoelectric, capacitive, or hydraulic pressure sensors, or low-quality load cells, which lose their ability to adjust after only a few years of use.
INDEPENDENT OPERATION OF EACH SENSOR
We do not use summing boxes in our instruments. Our proprietary electronics are capable of acquiring the individual signals of up to 20 load cells in parallel and simultaneously. We monitor each sensor during the weighing process to ensure we always provide the best possible measurement, detecting saturation, short circuits, unwanted traction states and other potential problems before giving a weight value that may not be of our trademark quality.
GREATER PRECISION
LONGER SERVICE LIFE
GUARANTEE 2 YEARS
IMPROVED USABILITY
LESS MAINTENANCE
UPGRADEABLE FIRMWARE
BETTER INTEGRATION
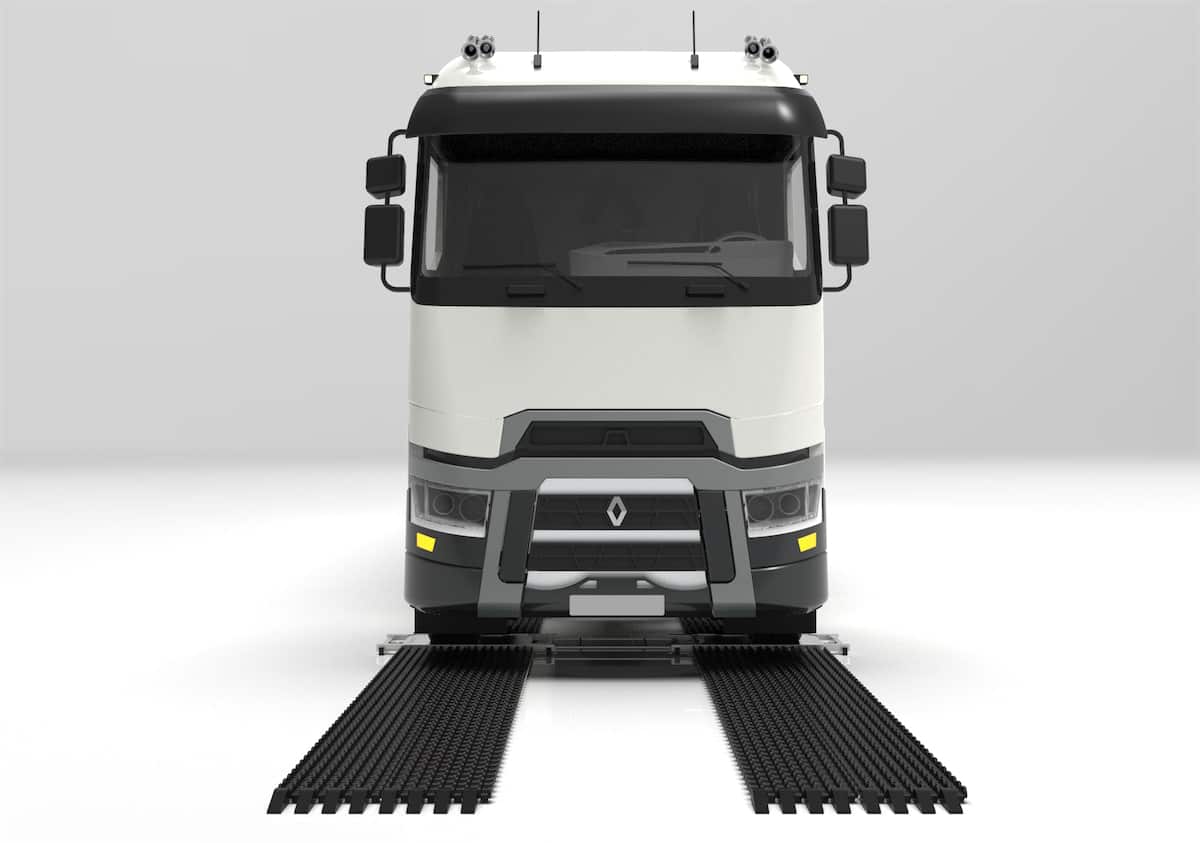
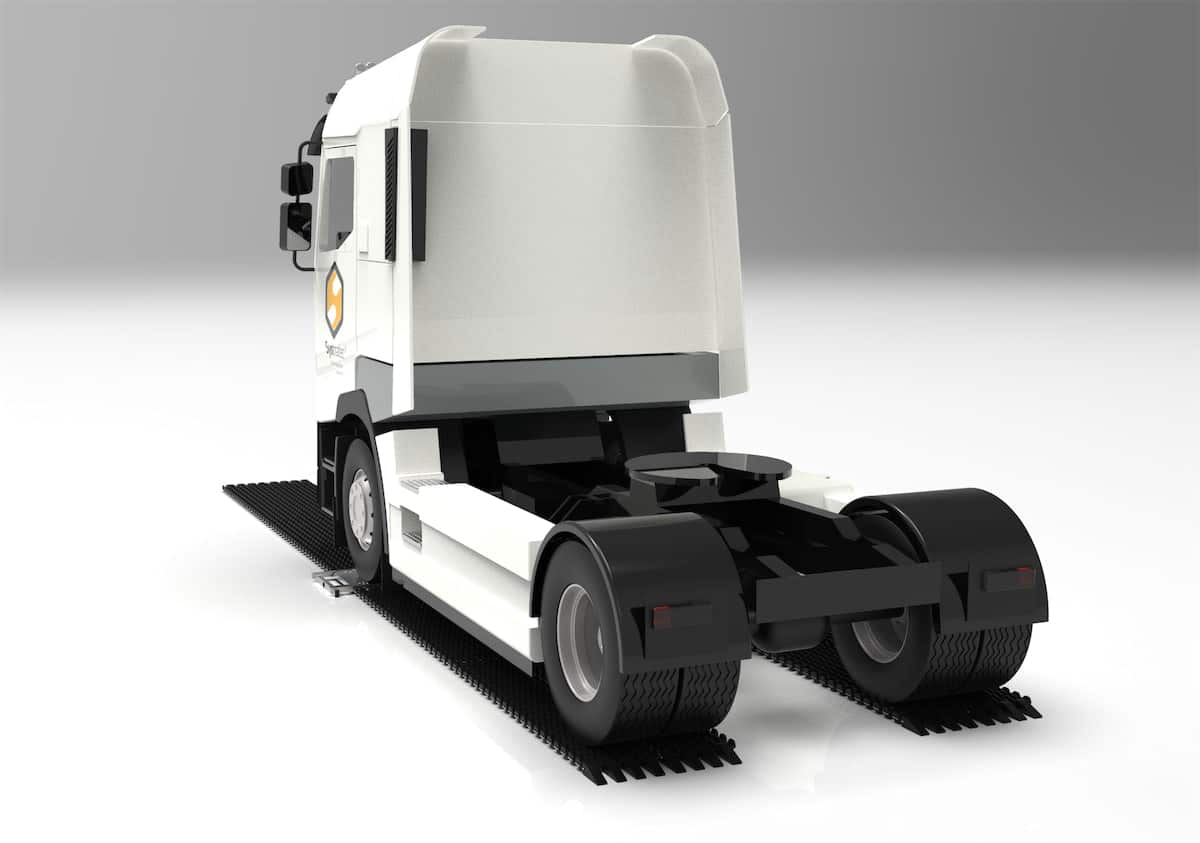
Do you need more information?
If you have any questions or need further information, please do not hesitate to contact us.