Auto|WS is the ideal platform scale weighing system for those who need to accurately measure weight and weight distribution on aircraft up to 1000kg per wheel.
Its footprint size and range make it an affordable solution for weighing and measuring the centre of gravity of light and ultra-light aircraft during construction or maintenance work.
Both the ramps and the weighing platforms of which it is composed are light and of contained dimensions, perfectly suited to be operated by a single person comfortably and quickly.
THE LOAD RECEIVING PLATFORMS
The scales or load receptor platforms are made of machined, seamless, aeronautical grade aluminium monobloc. The choice of material, as well as the elaborate internal structure, ensure rigid behaviour when applying the nominal load on a surface equivalent to the tyre footprint, avoiding the appearance of non-vertical force components.
The sensors chosen to equip each platform are high-end HBM bending load cells, mounted with height-adjustable feet.
The chosen connectors are of extraordinary quality, made of steel, equipped with a self-centring mechanism and automatic locking.
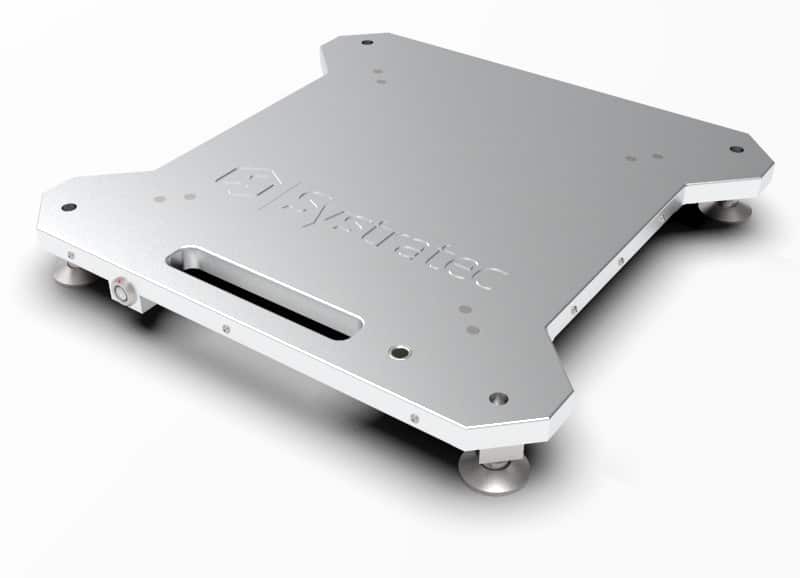
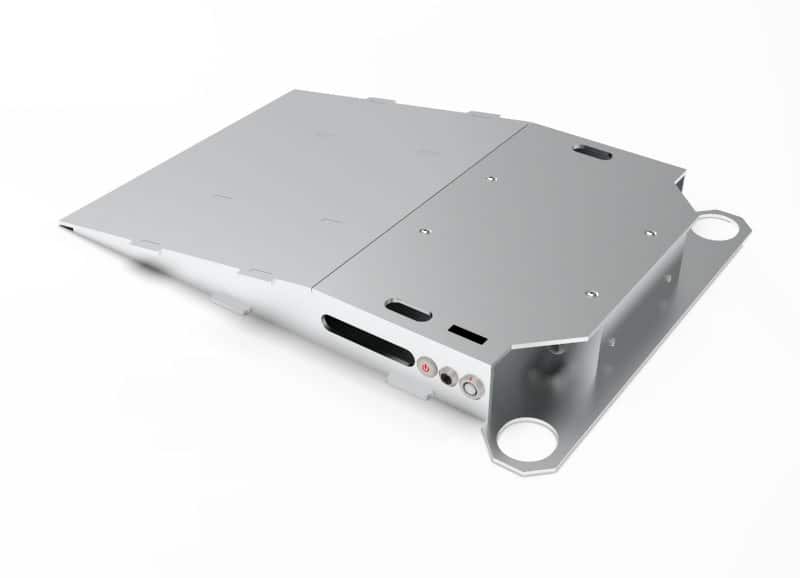
ACCESS RAMPS
The access ramps are made of welded aeronautical grade aluminium, with high strength and light weight for easy handling during installation.
Its unique shape allows easy towing of the aircraft on the system. It also has a smooth transition zone between the ramp and the load receptor platform, which ensures the best application of weight on the platform and results in a longer service life for the system as a whole.
In wireless configuration, they house the acquisition and processing electronics of their associated platform.
Two configurations depending on your needs and preferences: wireless or wired.
WIRELESS CONFIGURATION
We install a Systratec CORE measurement electronics and a Systratec LCGRID acquisition module inside each access ramp, which will process the signals from the HBM load cells on its associated platform to accurately measure the weight and point of application of the reaction on the platform. A rechargeable LiFePO4 battery is also installed in each ramp to provide more than eight hours of continuous operation. All data measured by the platform set is transmitted via WiFi or Bluetooth LE in real time to a display case for the operator.
WIRED CONFIGURATION
In this configuration the ramps contain no electronics, and the signals from the HBM load cells are carried by cable to an operator case containing Systratec CORE processing electronics with as many Systratec LCGRID acquisition modules as there are platforms in the system.
The operator can control the entire system from the touch screen of this self-contained, rechargeable case, as well as view the measurement results in real time and print out a ticket with all the measurement data.
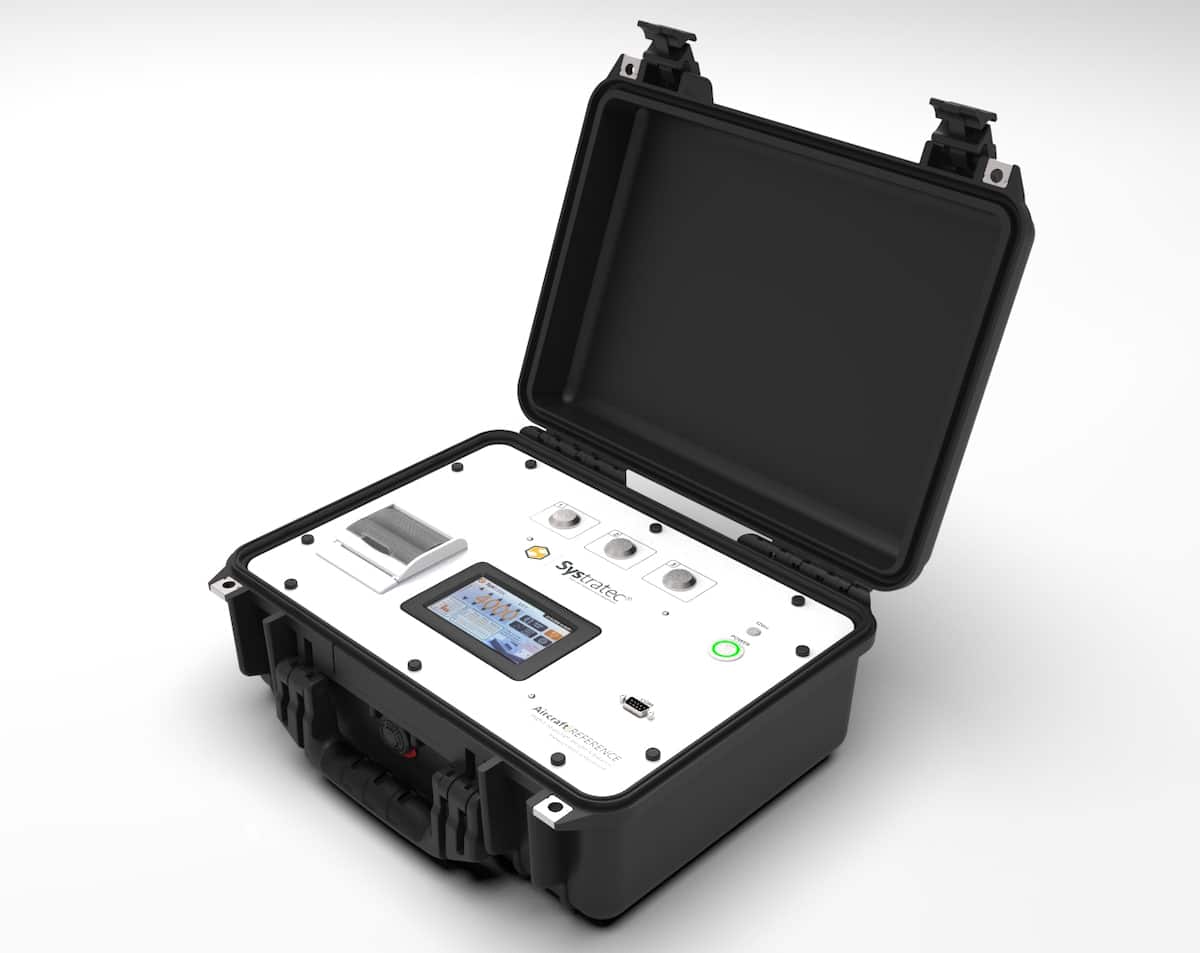
CONTROL AND VISUALISATION CASE
The system is remotely controlled from a SYSTRATEC aircraft|REFERENCE control and display case.
In wired configuration, the individual signals from all the system’s load cells are routed to the case for acquisition and processing by the Systratec CORE + Systratec LCGRID electronics inside.
In wireless configuration, the case connects bi-directionally via Bluetooth LE to the platforms’ electronics to receive all data and measurements in real time.
The case is equipped with a TFT colour touch screen for clear and simple operation of the system. It also has a thermal printer to obtain a hard copy of the weight and position data of the load on each connected platform.
The rechargeable LiFePO4 technology battery inside the case provides more than 8 hours of continuous operation.
MEASUREMENT OF WEIGHT AND CENTRE OF GRAVITY
Auto|WS platform scales benefit greatly from the advanced signal processing inherent in all our instruments equipped with Systratec CORE + Systratec LCGRID electronics.
We continuously monitor the signal coming from each load cell, amplifying it by means of zero-drift instrumentation operational amplifiers and then attacking the digitisation stage by means of noise-free 24-bit sigma-delta converters. The digitised signal is processed by DSP algorithms and evaluated for quality and then converted to weight values by applying the multi-point calibration parameters stored in the system.
The individualised and simultaneous access to each load cell is the start of our exclusive algorithm for calculating the centre of gravity, which allows the exact position of the load on the platform to be known in X and Y coordinates with millimetric precision.
The combination of these unique SYSTRATEC technologies ensures that each weight value and XY position of the load delivered by the system corresponds to a perfect measurement.
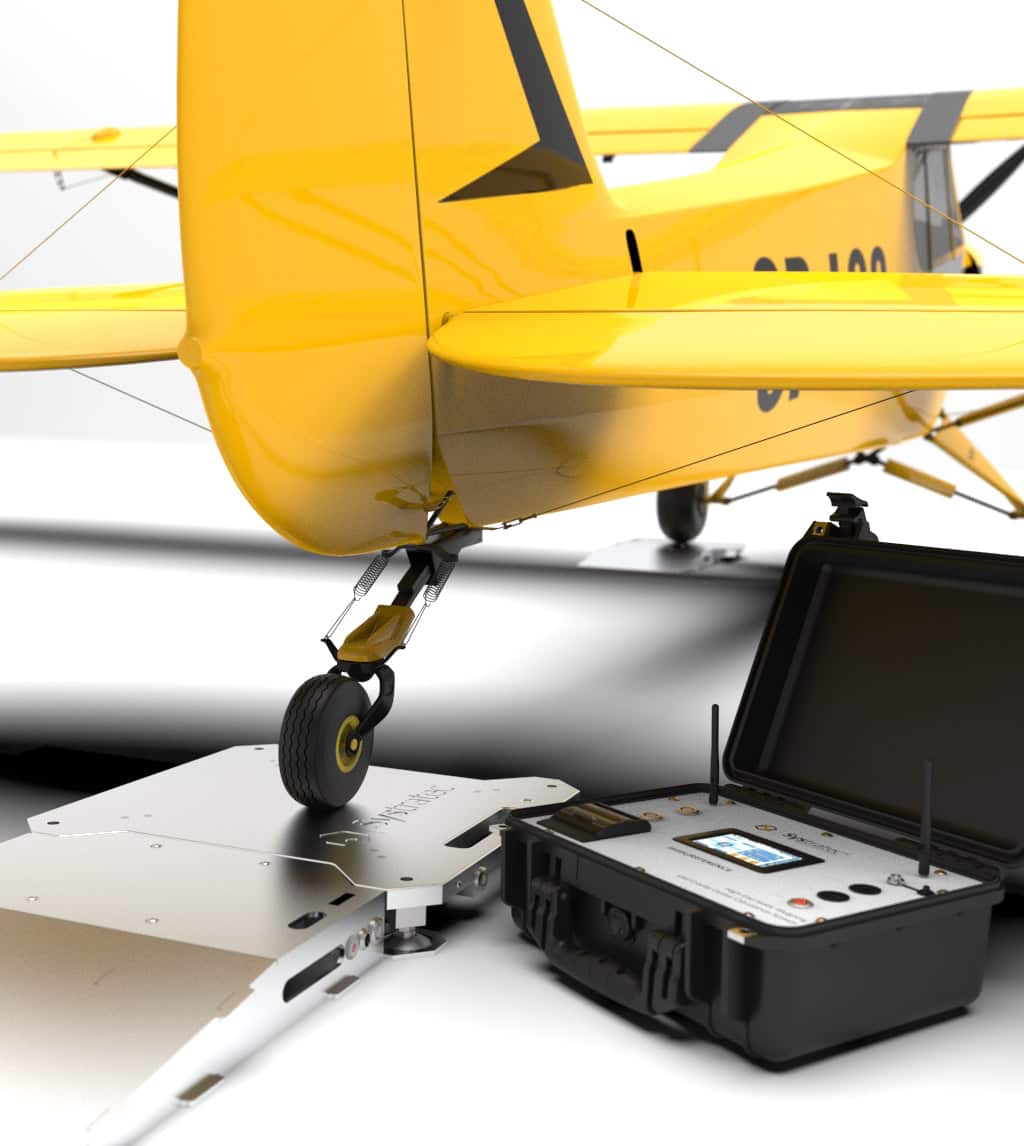
MAJOR INNOVATIONS
The Auto|WS weighing system incorporates the following technologies exclusive to SYSTRATEC:
ULTRA-RIGID STRUCTURE
The choice of material and the elaborate interior structure eliminate the bending effect so common in other platform systems by applying the nominal load on a surface equivalent to the tyre’s footprint. This improves the linearity of the instrument and the accuracy of the measurements.
ELECTRONICALLY ASSISTED INSTALLATION
Intelligent firmware routine to help the user to reproduce the mechanical conditions of the calibration laboratory every time the platform is installed for weighing. Visual indications through the control case for the adjustment procedure of the support feet, increasing the precision of the measurements.
SENSORS' BALANCE SURVEILLANCE
Intelligent firmware algorithm that continuously checks the signals received from each of the four sensors available per platform This unique feature detects abnormal signal variations in real time, identifying and indicating possible sensor failure when the load is on the platform.
INDIVIDUAL SHORT-CIRCUIT AND OPEN-CIRCUIT CONTROL
Continuous firmware process that detects sensor short circuit or open circuit failure conditions, also identifying the sensor in question and avoiding taking inaccurate measurements with the instrument.
LABORATORY QUALITY ELECTRONICS
Separate amplification and acquisition stages for each load cell, with operational zero drift instrumentation amplifiers and 24-bit noise immune sigma-delta converters. Fully customisable communications protocol via WiFi, Bluetooth® and/or serial interface for easy industrial integration and/or remote control.
AUTOMATIC CALIBRATION CHECK
Every time the platform is switched on, this exclusive firmware routine checks some parameters and compares them with the original values stored during calibration in our laboratory, detecting possible deviations that could affect the accuracy of the measurements.
INDIVIDUAL CONTROL OF TRACTION AND SATURATION
This firmware routine continuously monitors for possible saturation or an undesirable traction condition of the sensor due, for example, to mechanical locking of the platform by external objects, tools or accessories. It also identifies the sensor in question, facilitating early corrective maintenance.
HIGH-END SENSORS
HBM high-end OIML-certified stainless steel load cells for harsh environments, manufactured in Europe under the strictest quality standards, guaranteeing perfect performance throughout the life of the instrument.
DIMENSIONS
We manufacture our Auto|WS platform weighing system to the standard dimensions shown in the figure. In special cases we can manufacture the system to measure, if required.
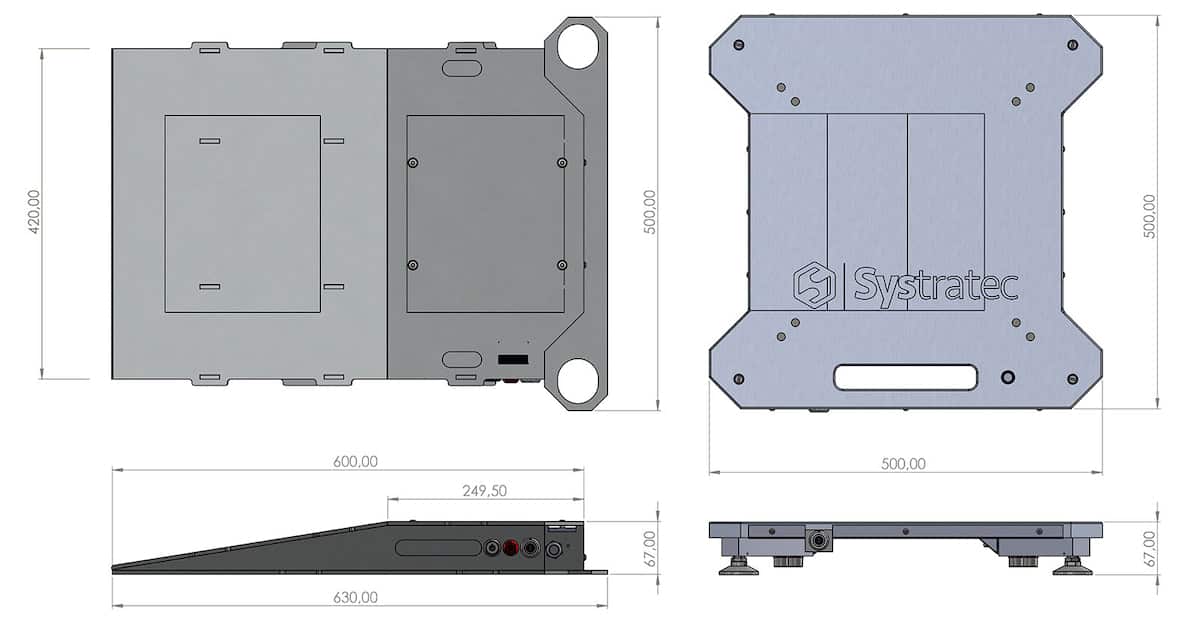
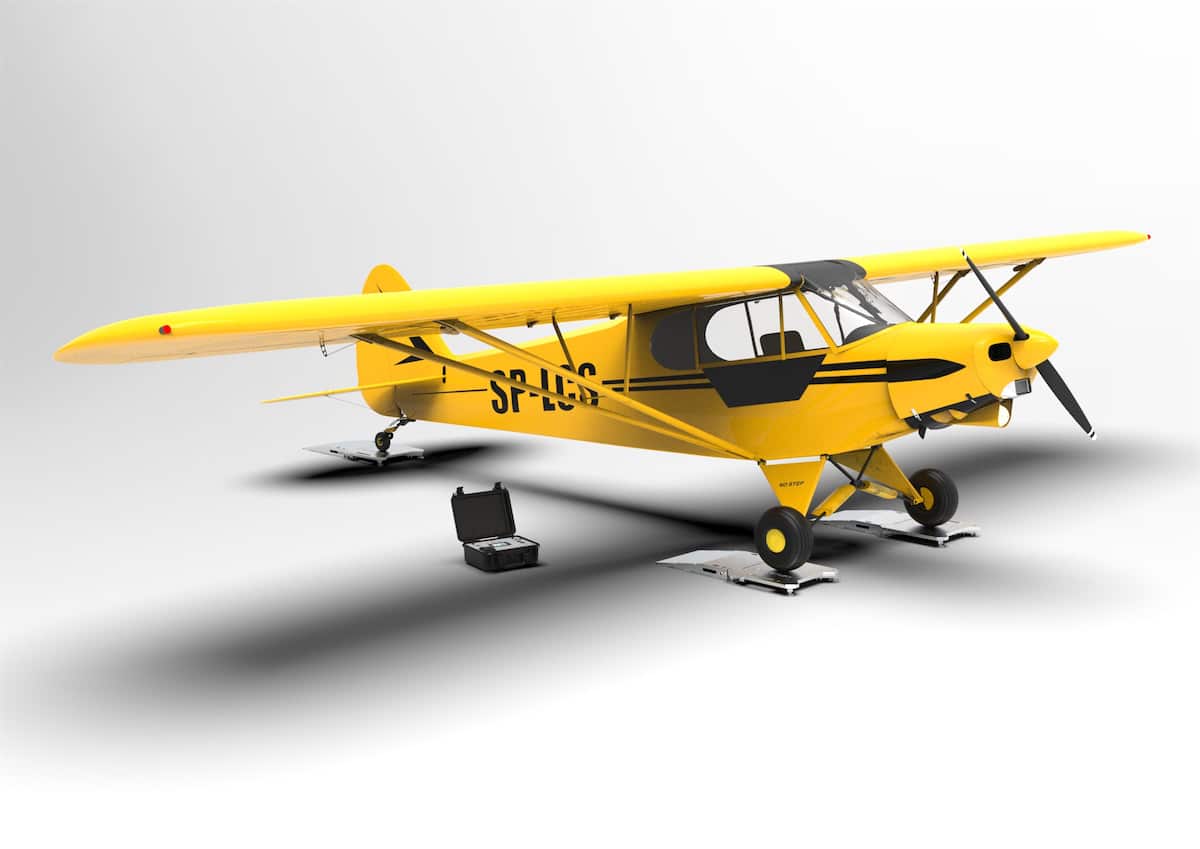
Aeroplane or medium helicopter?
Aero|WS System
The standard in portable weighing systems for helicopters and medium aircraft.
Heavy aircraft?
CARBON|aero Reference
The most advanced portable Centre of Gravity Weighing and Calculation system in the aviation industry.
On-Jack Weighing?
Jack|WS System
Convert your traditional lifting jacks into a weight & balance measurement system.
An embedded system?
Discover our fixed recessed system for aeronautical weight & balance measuring in FAL or specific hangar.
Need more information?
If you have any questions, need further information or would like to receive a personalised offer, please do not hesitate to contact us.