Jack|WS is SYSTRATEC’s proposal for converting your traditional lifting jacks into a high-end aircraft weight & balance measuring system. It consists of a set of three industry-leading HBM force sensors, the necessary adapters for your jack and aircraft model, and our well-known aircraft|REFERENCE electronics with firmware specifically adapted to the application.
The complete kit, with all its accessories, is housed in a military-grade PeliCase that allows it to be easily transported from one location to another, while perfectly protecting all components.
In native mode, it allows direct readout of the force supported by each jack, the total force exerted by the aircraft on the jacks, the X-coordinate of the centre of gravity in millimetres and the total moment of the aircraft relative to 25% of the mean aerodynamic chord, as well as the X-position of the centre of gravity in percent of the mean aerodynamic chord. In conversion mode, it provides the same information in units of mass, using the local gravity acceleration values stored by the system.
FORCE SENSORS
The force sensors chosen for this system are from the U10 family of sensors from the German manufacturer HBM. This family of sensors is the reference in the industry for force measurement, due to its extraordinary precision, repeatability and durability.
We select the range of sensors from the wide range available depending on the customer’s needs, being able to connect sensors from different ranges at the same time, usually with a shorter range on the nose jack and a longer range on the main jacks. Capacities available are 1.25kN, 2.5kN, 5kN, 12.5kN, 25kN, 50kN, 125kN, 250kN and 500kN (approximately 125kg, 250kg, 500kg, 1250kg, 2500kg, 5000kg, 12500kg, 25000kg and 50000kg).
This wide range of available capacities allows us to configure the system to weigh virtually any aircraft on the market.
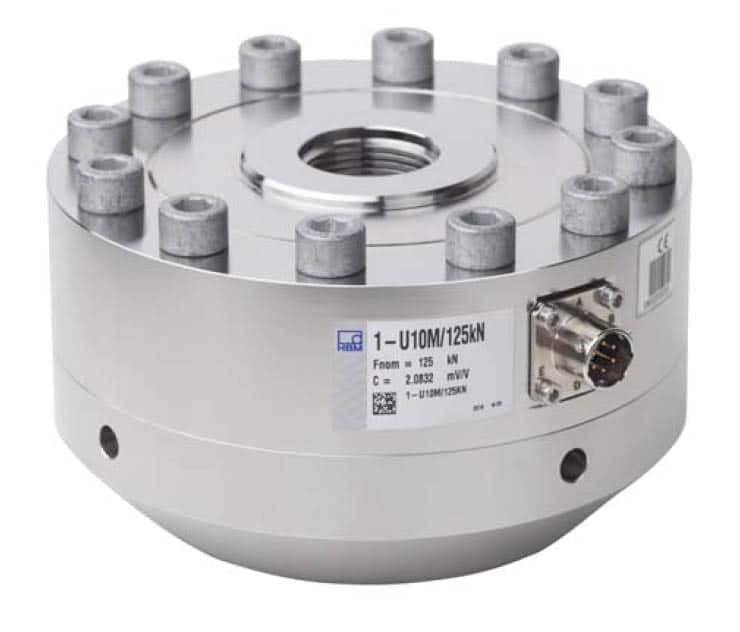
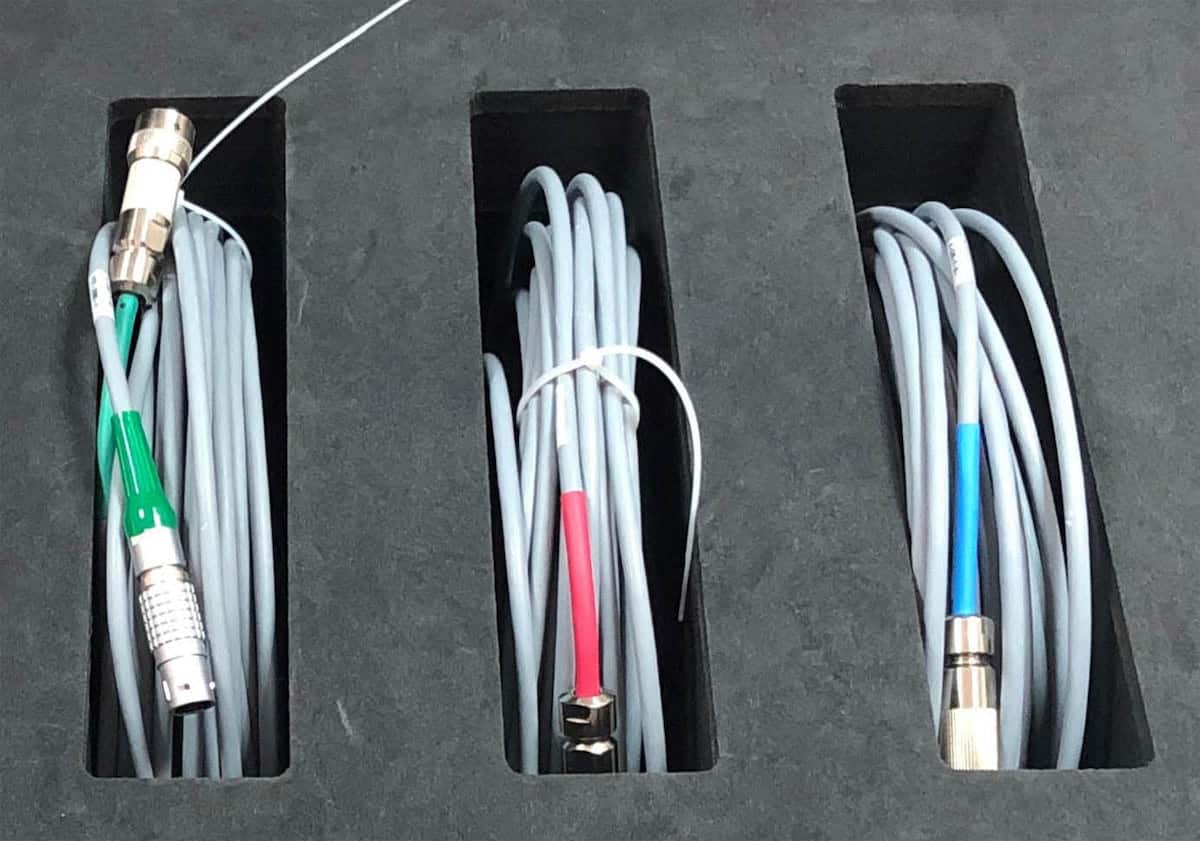
SIGNAL CABLES
The signal cables linking the sensors to the measurement electronics are six-wire twisted plus shield, allowing the system to be built in a ratiometric configuration. They have an ITT bayonet connector on the sensor end and a LEMO connector with interlocking on the measurement electronics side.
The cables are marked with different colours for each sensor, ensuring that each sensor is used with the cable with which it was calibrated, because every detail is important when it comes to delivering the highest possible measurement accuracy.
TOP AND BOTTOM ADAPTERS
Each force sensor must be equipped with a top and bottom adapters, which are hand-tightened to the sensor body and which are interchangeable by the user in case of a heterogeneous aircraft fleet.
The upper adapter is manufactured according to the specifications of the aircraft to be weighed. It usually has a hemispherical cup shape, the most common for making contact at the lifting points on aircraft jacks, with dimensions and tolerances varying from case to case.
The lower adapter is manufactured according to the specifications of the lifting jack used. It usually has a cylindrical female shape, to be placed as a sleeve on the jack jack shaft.
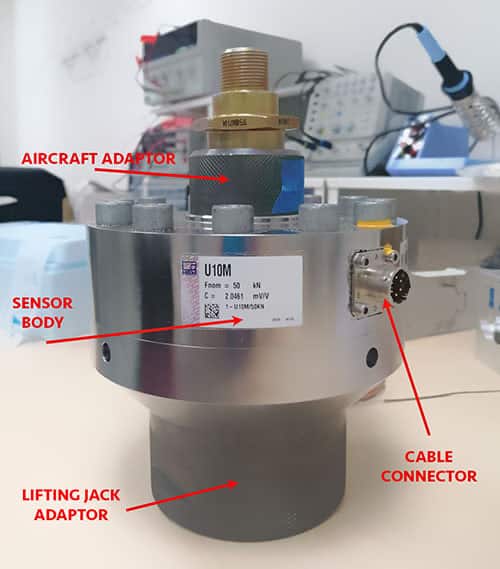
SYSTRATEC Aircraft|REFERENCE measurement electronics
The measuring and processing tasks are entrusted to an Aircraft|REFERENCE electronics in PeliCase format. This electronics is stored together with the rest of the system components and is calibrated to be used exclusively with the force sensors belonging to it. Its fundamental characteristics and performance are as follows:
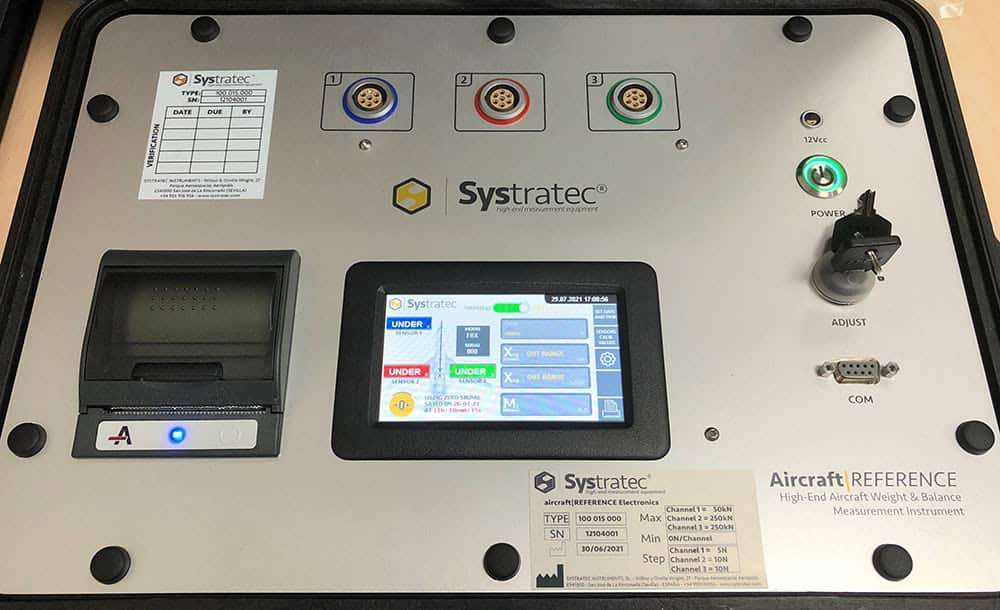
PUSHBUTTONS AND CONNECTORS
The connectors chosen for the coupling of the measurement cables are from the manufacturer LEMO, of the highest quality and robustness. The rest of the pushbuttons and connectors have been chosen with the same care to avoid any failure during the life of the system. We also incorporate a key switch to protect access to all the essential metrological configuration functions of the equipment.
INTERNAL ELECTRONICS
The aircraft|REFERENCE electronics benefit greatly from the advanced signal processing inherent in all our instruments equipped with Systratec CORE + Systratec LCGRID electronics. We continuously monitor the signal coming from each load cell, amplifying it by means of zero-drift instrumentation operational amplifiers and then attacking the digitisation stage by means of noise-free 24-bit sigma-delta converters. The digitised signal is processed by DSP algorithms and evaluated for quality and then converted to weight values by applying the multi-point calibration parameters stored in the system.
An internal rechargeable LiFePO4 battery powers the entire system. It provides a continuous operating time of eight hours and is fully recharged in 45 minutes.
VISUALISATION SCREEN
The integrated 4.3″ TFT touch screen is the system’s interface to the operator. All system configuration operations are performed from this full-colour display and allows clear, graphical display of all measured and calculated values by the system.
The graphical interface of the system has been carefully designed to present all measurements and calculations on a single main screen, combined with access buttons to the main configuration functions. It is available in English, Spanish and French.
The brightness and contrast values allow a perfect display whatever the lighting conditions of the environment. The touch panel used allows direct use or use with work gloves or external pointers.
PRINTER
The control electronics incorporate a thermal printer for real-time printout of all system measurements and calculations.
The printout identifies the serial number of the system and the date and time of the test. In addition, if included in the factory configuration, it indicates the location where the test is performed and the aircraft model with its serial number.
COMMUNICATIONS
We incorporate an industry-standard RS-485 serial bus, accessible via a DB-9 connector on the front panel.
Through this communications interface, the electronics send all the values measured and calculated by the system in real time once per second, as well as all the information necessary to unequivocally identify the weight & balance measurement.
The protocol of the frame used can be tailored to customer requirements if specified at the time of order.
Light Aircraft?
Auto|WS System
A new category in portable Weighing and Centre of Gravity Calculation systems for light and ultralight aircraft.
Aeroplane or medium helicopter?
Aero|WS System
The standard in portable weighing systems for helicopters and medium aircraft.
Heavy Aircraft?
CARBON|aero Reference
The most advanced mobile Centre of Gravity Weighing and Calculation system in the aviation industry.
An embedded system?
The fixed system for aeronautical weighing and centre of gravity calculation in FAL or dedicated hangar.
Need more information?
If you have any questions, need further information or would like to receive a personalised offer, please do not hesitate to contact us.