Embedded system for weighing and calculation of centre of gravity in weighing hangar or FAL
Case Study
Embedded systems for weighing and measuring aeronautical balance are the most suitable option for manufacturers and large fleet maintainers who have a specific hangar for weighing operations or who carry out this operation at a fixed station in the aircraft assembly process.
The main advantage of these systems is their accuracy, capable of surpassing the best portable platform. They can also be equipped with nose gear lifting systems for testing at different pitch angles and advanced integrations can be made with the customer’s IT infrastructure to fully automate the weighing cycle.
At SYSTRATEC we manufacture these systems completely tailored to the customer’s requirements, both in terms of dimensions and in terms of the number of scales or range of each scale. We also provide the necessary documentation and advice for their installation, in collaboration with the building maintenance company chosen by our clients. The SYSTRATEC team supervises the installation, integration and handover of the system on site, continuously accompanying all the teams involved from the very beginning of the project.
An example of such a system is presented below, designed to be installed on the Final Assembly Line of Airbus Military’s A400M aircraft:
The Challenge
- To measure aircraft weight and gravity center X coordinate in percentage of the Mean Aerodynamic Chord, in a full controlled weighing cycle, in less than 30mn per cycle.
- To ensure a maximum weight error of 100kg for a 150 000kg aircraft total weight, and a maximum error of 14mm for X COG coordinate measurement for a 45 meters nose to tail aircraft.
- To provide reliable industrial system interface to Final Assembly Lane external computer aided test system, to share measurement results, manage traceability, and to allow full remote control and weighing procedure quality auditory.
The Solution
- Seven Systratec REFERENCE platform scales, with a range of 30 000kg each, custom made to fit aircraft footprint in every configuration, equipped with High-End HBM Class III load cells controlled by seven Systratec CORE electronics with custom firmware and the required Systratec LCGrid expansion modules.
- Full automated lifting machine under nose landing gear platform, with its sensors and actuators managed by one Systratec CORE electronics, working together with a Systratec CORE based WiFi inclinometer, installed on the aircraft, to measure its pitch angle with 0.005º resolution.
- One Weighing Auxiliary Industrial Mean central cabinet to control the whole system, show and share the results, and able to accept remote commanding from external Computer Aided Tests Systems.
High-End aeronautical systems require same level documentation, tools and after sale services.
Detailed Weighing Procedure
Detailed Mechanical Maintenance Procedure
Detailed Metrological Maintenance Policy
Long term Spare Parts Policy
Custom Manufactured Control Tools
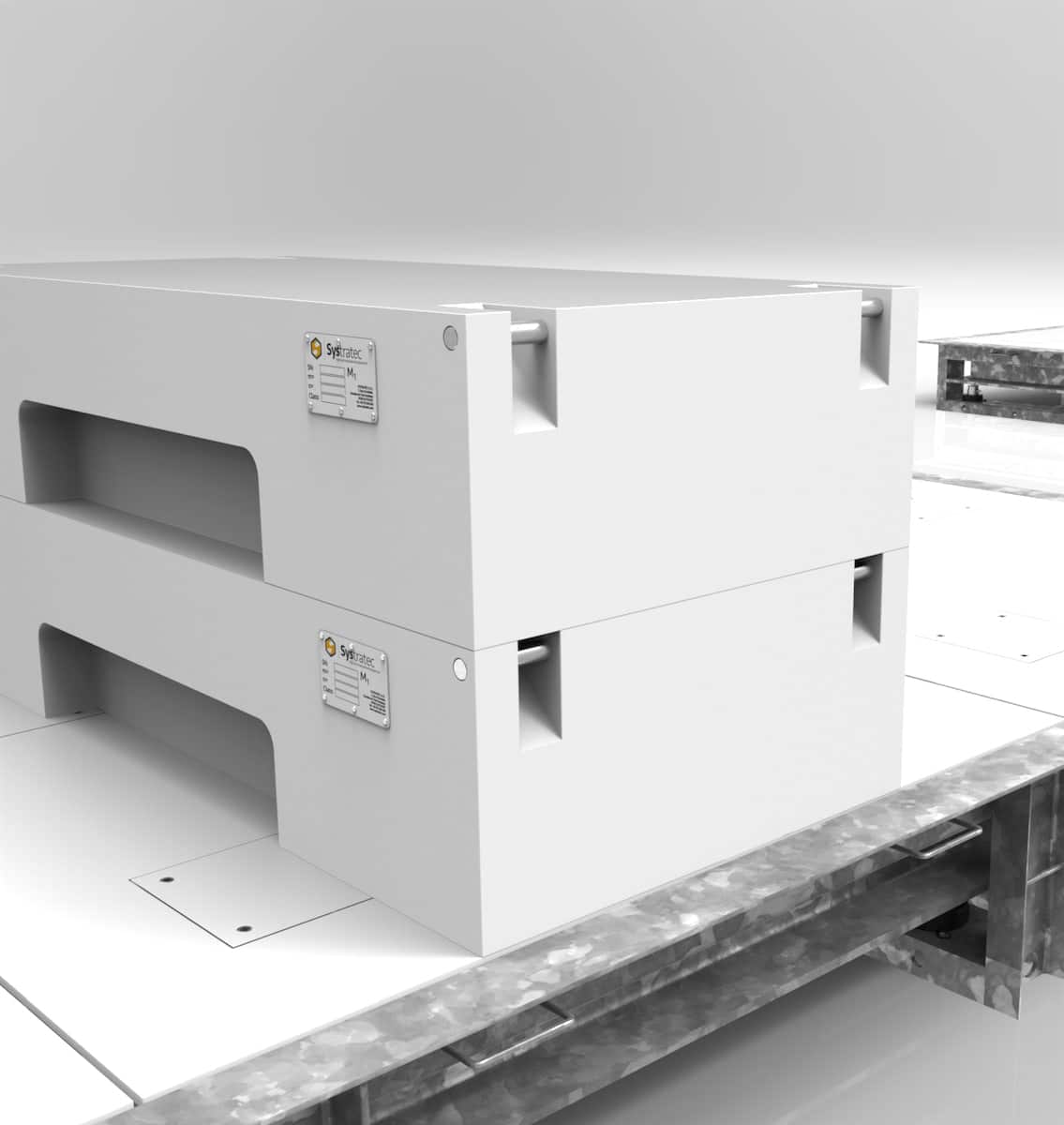
Engineering
Manufacturing
Installation
Calibration
The Result
In comparison with the ancient on-jack weighing and gravity center calculation method, with Systratec ground system you will obtain:
Accuracy improvements
Dynamic aircraft pitch adjustment during tests for special purposes.
Repeatability improvements
Work Safety Conditions Improvements
Measurement Uncertainty Reduction
Weighing cycle time reduction
Aeroplane or medium helicopter?
Aero|WS System
The standard in portable weighing systems for helicopters and medium aircraft.
Heavy aircraft?
CARBON|aero Reference
The most advanced portable Centre of Gravity Weighing and Calculation system in the aviation industry.
On-Jack Weighing?
Jack|WS System
Convert your traditional lifting jacks into a weight & balance measurement system.
Aeroplane or light helicopter?
Auto|WS System
A new category in portable Centre of Gravity Weighing and Calculation systems for light aircraft.